Allied Mask and Tooling is a secondary manufacturing company in Toledo, Ohio using their Gigabot in the production of parts for the automotive and medical industries. We talked with Jared Murray, Design Engineer and Project Manager, to understand more about how Gigabot has fit into their workflow and cut their costs.
Q. Can you explain the industry you’re in, the work Allied Mask and Tooling does, and how Gigabot fits into your process?
We are a secondary manufacturing company that is heavily involved in the automotive industry as well as the medical industry. We don’t normally deal directly with car companies such as Toyota or Ford, we deal with their customers. Their customers are typically molding, painting, metalizing, and assembling parts to get ready for the plant that will build the vehicles. We make sure that the equipment we use, like the heaters for plating tanks, are reliable and won’t cause any faults in our products. We are the customer of the customer of a major car company, which is referred to as secondary manufacturing. What we do is create tooling to hold parts to be painted or metalized. Metalizing is an aluminum coating that is on headlights and taillights and allows the light to be reflected. We also create paint or metalizing masks which allow only some of the part to be metalized or painted.
This is what a part looks like after metalizing and assembly.
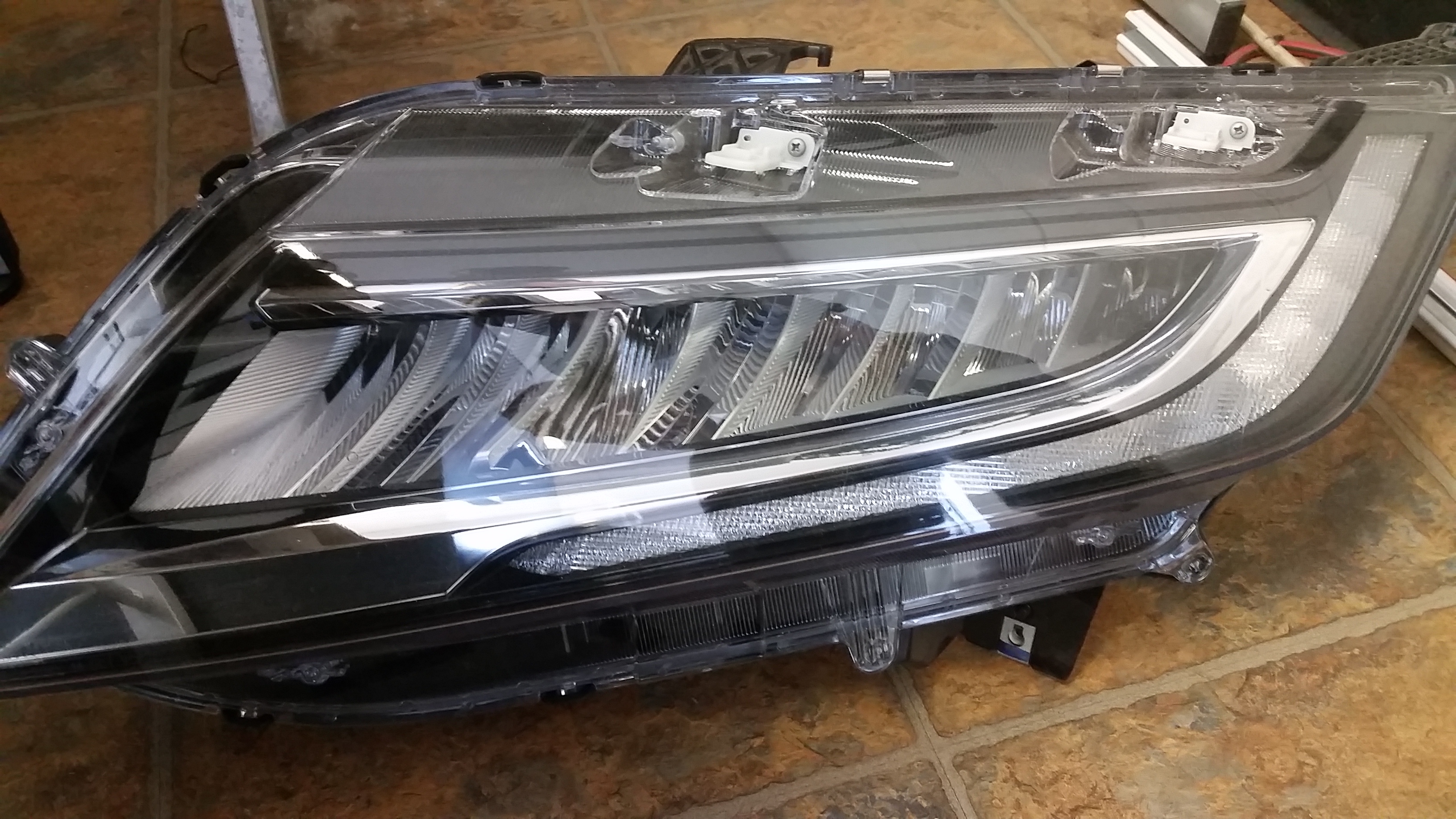
We are using our Gigabot to print out end-use parts as well as molds which I have designed in Solidworks to fit the parts and mask we want, which will then be used for plating in our nickel tank.
In this picture I have four molds on our printer that we are going to plate with nickel and cut out.
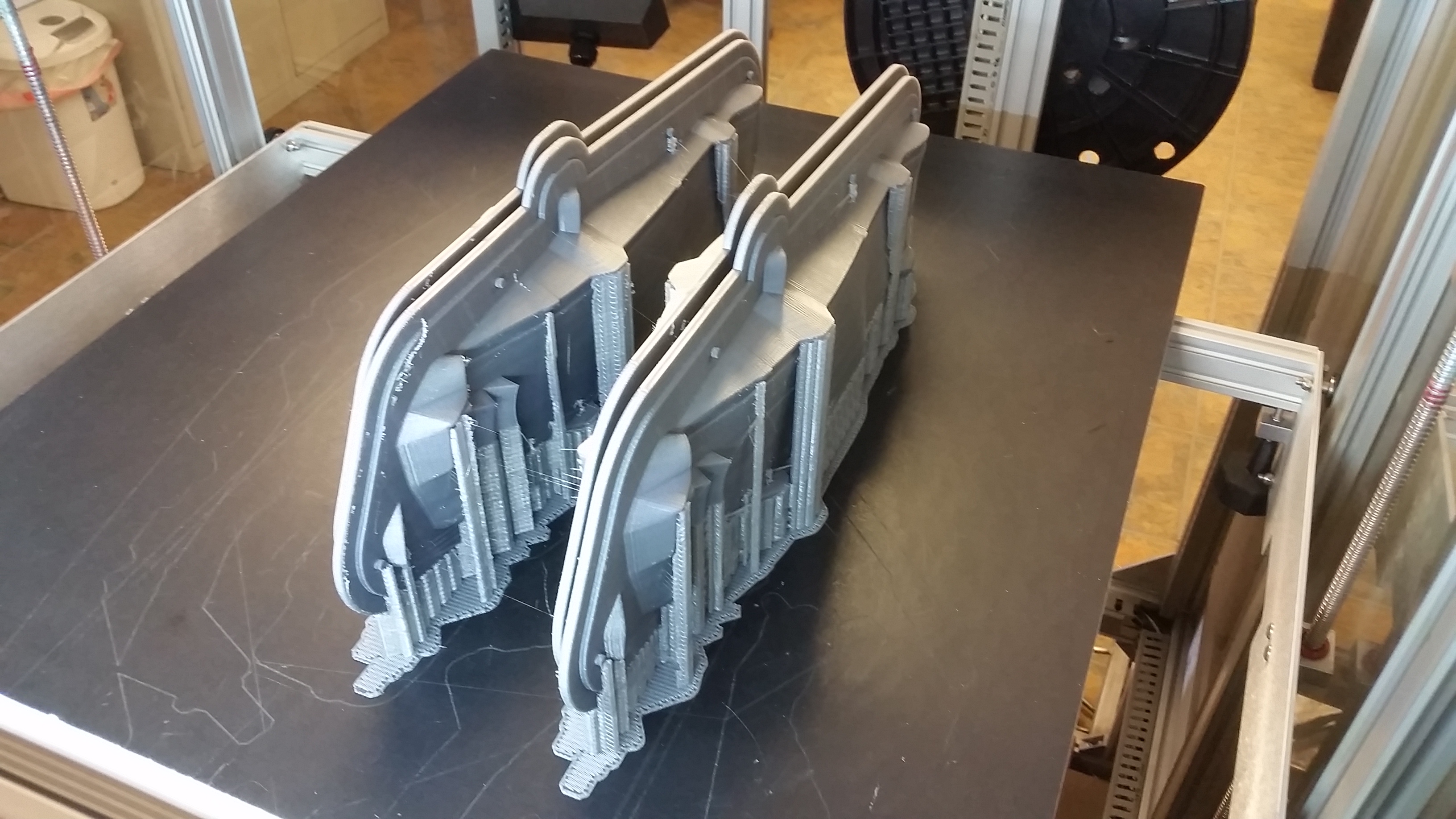
Q. How were you doing this work before you got your Gigabot?
Previous to having our Gigabot we use to have to wait until production-level parts were available. Then we would have to set up our nickel plating molds with a part and wax, and form the wax by hand to get it in the shape we wanted.
Doing it this way caused us many issues, one being that we had to wait to start our process until production parts were available. This meant our customer had to wait to produce until we were done with at least the first set, which could sometimes take up to six weeks.
Q. What brought you to 3D printing? Why did you start to investigate bringing this technology into your business?
Building on the last question, our customers were wanting us to produce production tooling before parts were even available. We then had one of our customers say that we had to produce our tooling with the 3D data only. At this time I was finishing up my CAD/CAM certificate and was wrapping up my second and last semester of Solidworks that our college provided. In this class, I started to learn about 3D printing and how it’s shaping the future. When our customer said that we could only go off the 3D data they provided, it got me thinking about the CNC classes I took and how expensive and time-consuming it would be to produce this via CNC out of plastics.
I kept coming back to the idea: “Why not just 3D print our molds for plating?” So, I talked to the boss about it and we had a couple of tests prints made by a local supplier, and we loved how our production-level parts fit into these prints. We then decided to design an entire job out of the 3D data and have it all 3D printed for us. The downside to this was the still-very expensive cost of having our larger part molds printed, and the time it took to get them shipped to us.
Q. Has 3D printing enabled you guys to take on jobs you couldn't otherwise perform?
Yes, the Gigabot has enabled us to take on more jobs and be able to hire people with less skill since I am now doing all the design and mold setup on it. I used to have to have multiple top-paid artists working with the wax and parts to make our plating molds. Now I can design the molds, design how we’re going to hold our molds in place, and design in clamps and anything else we need. Our new method using Gigabot allows us to do more ahead of time and make everything a lot more accurate.
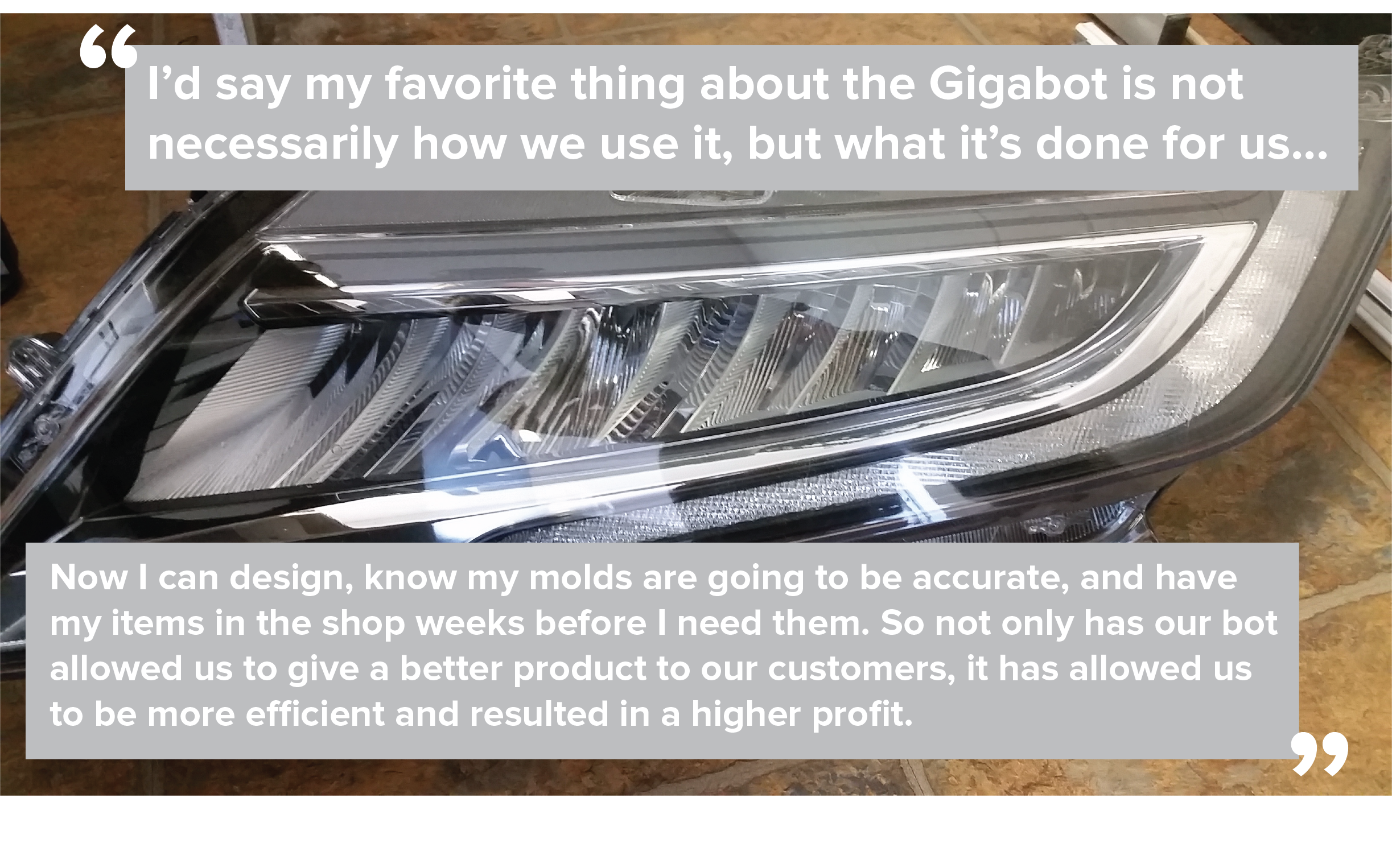
Q. Do you have an estimate of your time and/or cost savings using Gigabot versus your alternative options of manufacturing?
Contracting out 3D prints externally was very costly. For our first project when we started this whole idea of 3D printing for our plating molds, we spent nearly $40k on just the prints. We were researching 3D printers, but every printer that was remotely affordable had way too small of a build envelope, or it had a large-enough print volume but cost close to what our annual sales were at the time. Printing large parts in many pieces and paying that much out just couldn’t be done, and potentially forking out $40k every project for our larger parts was just not feasible. We were in a dilemma.
I researched for a few weeks and came across a video of a Gigabot printing large-scale parts at an affordable price. For the first time in a couple of months I got excited that our new thought process on how to use a 3D printer was going to become a reality. And that’s when I contacted re:3D.
So, even purchasing the Gigabot compared to what we paid for prints has saved us a lot of money over the last year or so that we’ve had our bot.
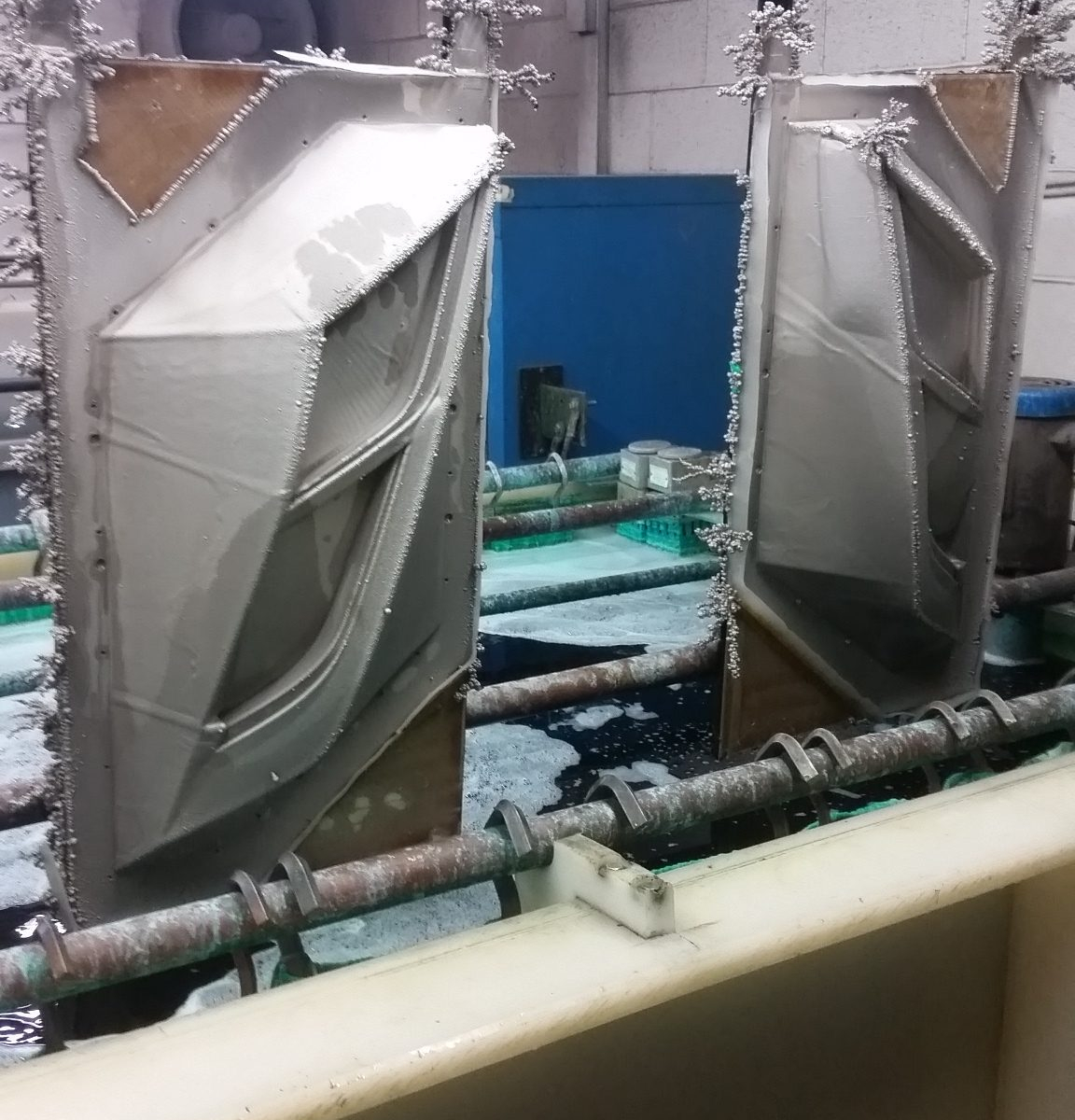
Q. Favorite part about using Gigabot?
I’d say my favorite thing about the Gigabot is not necessarily how we use it, but what it’s done for us. In having the bot, we are now a lot more organized and getting more jobs shipped out on time and even early. Elaborating on that, by having the bot and being able to do what we do with it, it’s allowed me to design entire jobs on Solidworks, which allows me to order things ahead of when the guys will need them. We used to have to design and try to order after we started working on a project and know what the hand layout of our wax molds would look like. This would force all of our orders to be on a rushed delivery, which would cost us more and give us a lot more to stress out about if things didn’t go as planned.
Now I can design, know my molds are going to be accurate, and have my items in the shop weeks before I need them. So not only has our bot allowed us to give a better product to our customers, it has allowed us to be more efficient and resulted in a higher profit.
Morgan Hamel
Blog Post Author